Mechanical working:
critical points
Some insights based on practical cases
Consumption of jewelry produced by plastic deformation
From 2017 Gold Survey and 2017 World Silver Survey data consumptions, it counts a gold consumption equal to 1900 tons worldwide and silver equal to 8059 tons worldwide (6438 of which used in the jewelry sector and 1621 in the silverware sector). Assuming a 60% proportion, 1150 tons of gold and 4500 tons of silver are transformed in jewelry through plastic deformation.
Plastic deformation process advantages
Some of the advantages of a plastic deformation process are unique among the technologies used nowadays and are:
- Compact surface, recostruction of crystalline grain
- High mechanical resistance
- Automation of repetitive operations, high productivity
- Low thicknesses
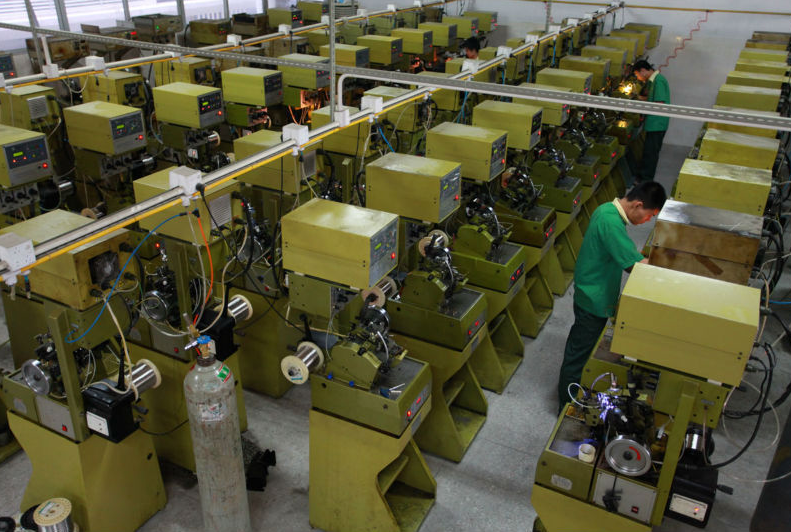
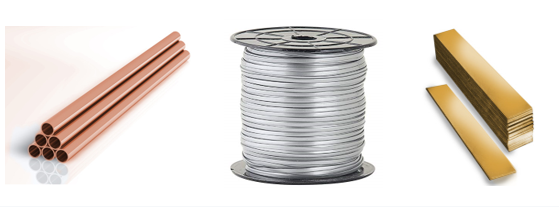
One of the problems that need to be faced is the wide variety of productive processes in the plastic deformation field that allow to obtain the same final objects starting from three types of semi-finished: sheet, wire and tube.
These semi-finished can we worked in totally different manners. The choice of the kind of working comes from the specific aim and type of production.
The aim of this speech is, starting from some examples of problems found, identify the causes and the proposed solutions, while discussing some general causes and problems.
Frequent problems during production
The most common problems regarding the production of the item are:
- Brittleness, unsatisfactory deformability
- Unsatisfactory mechanical properties
- Problems with tooling machineries
- Residual stresses, not compliant tolerances
- Soldering
- Hollowing
Soldering and hollowing are not properly plastic deformation processes, but they are much influenced by the semi-finished.
Frequent problems: final product
Among the problems related to the final product we find:
- Cracking over time (stress-corrosion cracking)
- Loss of elasticity («spring effect» missing)
- Surface wear
The first case is a brittleness problem on 750‰ red gold bar produced by casting. The initial semi-finished had a relatively important thickness which, for this kind of alloy, caused a heat dissipation problem. In this case the die had the traditional passive heating used in continuous castings (where the die absorbs the heat of the metal flowing inside). This kind of cooling system, particularly for 18 carat red gold, can cause formation of fragile intermetallic compounds when temperature is lower than 400° degrees so that, keeping a pretty thick object for enough time at medium-high temperatures (lower than the casting phase, but higher than ambient temperature), the bar could become brittle. This is sometimes visible not at first but in the lamination phase showing surface flakings or crackings.
In the case of red gold the solution is to cool the item as soon as possible in order to avoid heat dissipation through the adoption of a thinner die (in this case we passed from a 10 mm to a 7 mm thickness), by accelerating the lowering of the bar to avoid formation of intermetallic compounds and, in case the air wasn’t able alone to dissipate the heat, introduce a water cooling system.
Preparation of ingots works similarly: the problem of heat dissipation is the same and can cause brittleness.
Casting and solidification: critical points
Among the casting phase critical points we find:
- Casting time
- Presence of a pre-casting
- Type of crucible (brittleness problems have been noticed resulting from use of silicon carbide crubles which release silicon in the alloy making it brittle)
- Casting quantity
- Ingot pouring: importance of pre-heating at 250-300°C to avoid thermal shock
- Section of semi-finished needs to be chosen according to the kind of object to be obtained. It would be necessary to complete at least 2 cycles of reduction and annealing (for example sheet 0.2 mm ß 0.67 mm ß 2.2 mm ß 7.5 mm)
The preparation phase which involved joining gold with iron didn’t have any problem.
The only problem have been the chain crackings during workings following formation: the sheet didn’t present the necessary ductility to absorb the bending phase of the semi-finished (insufficient mechanical strength).
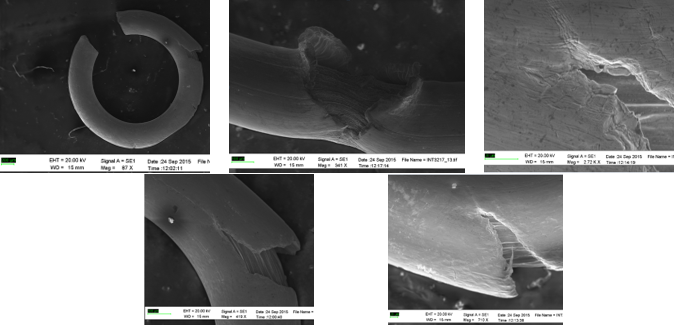
We started our survey looking for data on deformation and reduction phase.
The initial process undertaken by our client, where our sheet was taken to 0,4 mm and then wrapped, was preceded by two lamination phases which didn’t complete that homogeneous transformation necessary for the sheet to have an adequate microstructure.
The inhomogeneity during reduction creates a residual stress state.
Our advice was to unite the two phases and follow out a lower number of deformation cycles.
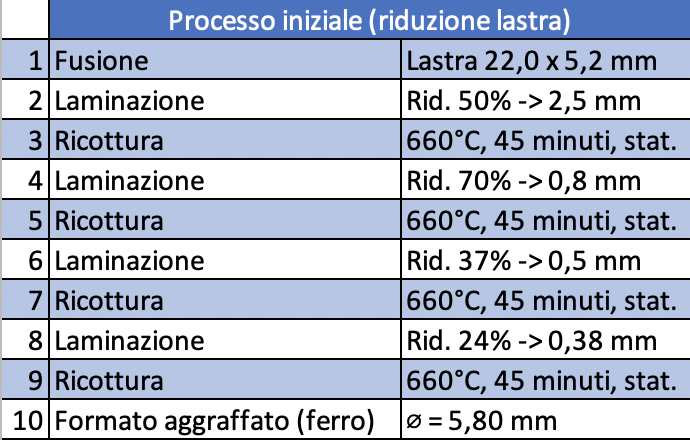
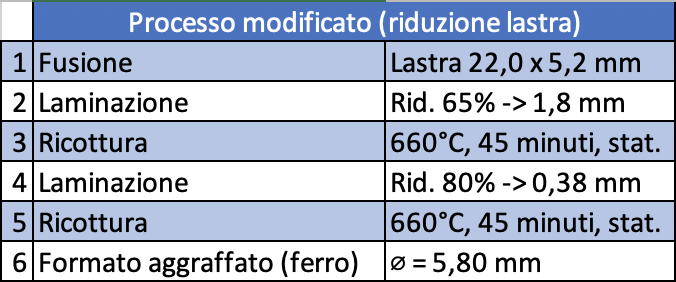
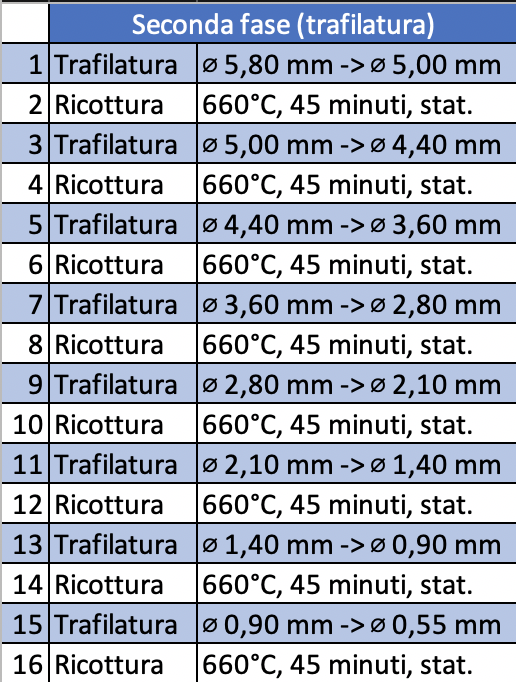
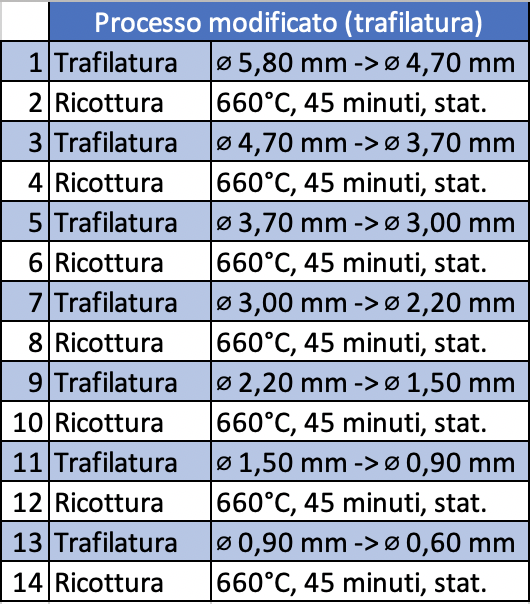
Critical point: plastic deformation process
In conclusion, the cause of the problem is the inhomogeneities in sheet reduction degrees.
The corrective action has been a lower number of deformation cycles, with the aim of making the microstructure more homogeneous.
A further advantage has been a time reduction on the production cycle.
Critical point: degree of reduction before annealing
Reduction: critical points
The critical passage of the case mentioned above has been the reduction level before annealing.
As far as the general aspect of reduction plastic deformation, it’s necessary to pay particular attention to:
- Type of semi-finished (wire, sheet, tube) and size
- Reduction degree calculation, to be defined starting from the final product to be obtained
- Machines: size, power and condition
A good microstructure is to be preferred rather just a hardness measure.
Area reduction calculation
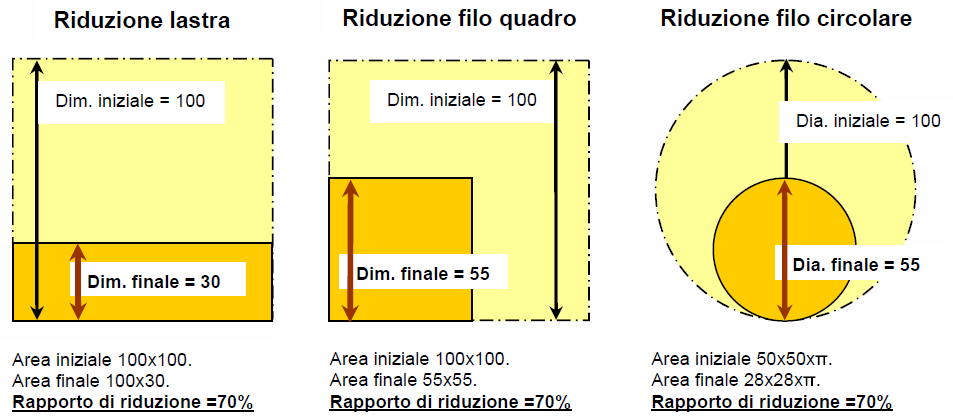
Riduzione: punti critici
Rolling mill size modifies the stress state:
- Small-sized rolls and/or small deformations tend to deform metal more on the surface than at its core, inducing a surface tension state
- Big-sized rolls tend to deform metal more ai its core, inducing a surface tension state
A residual stress inside the piece is inevitable. The amount is controlled through mechanical deformation and thermal treatments.
SURFACE RESIDUAL STRESS, ESPECIALLY WITH COARSE GRAINS: allows crack openings and can be connected to stress corrosion cracking.
Something silmilar goes for drawing where on one hand there is a radial stress and on the other a tensional stress.
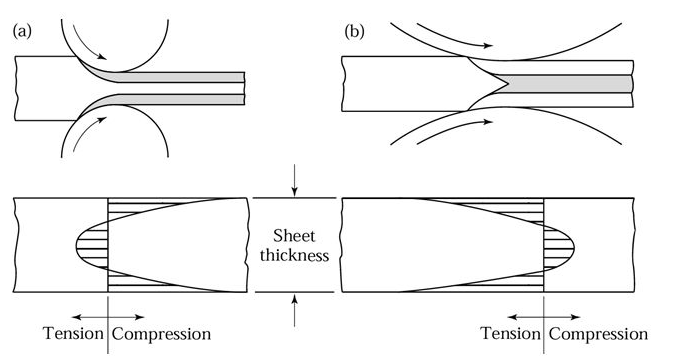
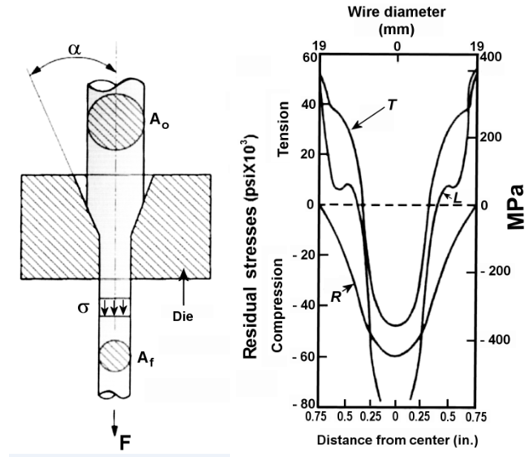
In this case the items are produced at the same way and photographed at SEM/EDX during production phase (after hollowing).
Sample 1: grain refined alloy
Sample 1 is an alloy containing a gran refiner, a substance that makes the alloy more compact increasing the nucleation points both during the casting phase both during annealing.
Sample 2: alloy without grain refiner
Sample 2 and sample 1 present the same object. They are produced at the same way but sample 2 is an alloy without grain refiner. It’s noticeable a slight surface roughness.
This element is to be taken into account from an operational and economical point of view. Under the same conditions, some formulations allow a better compactness of grain refiner.
If the addition of grain refiner is compatible with production cost, it’s advised to proceed with a change in formulation.
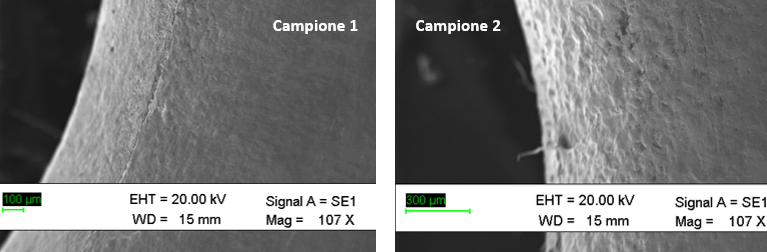
Critical element: alloy formulation
Other case where we can find different microstructures of a refined and not refined alloy, it can be noticed on the grain of a semifinished in a cold worked state. For example a wedding ring. The number of grain refiners is higher per area unit in the alloy with refiner, which makes the grain more compact, allowing a better resistance to possible cracks (sample 3).
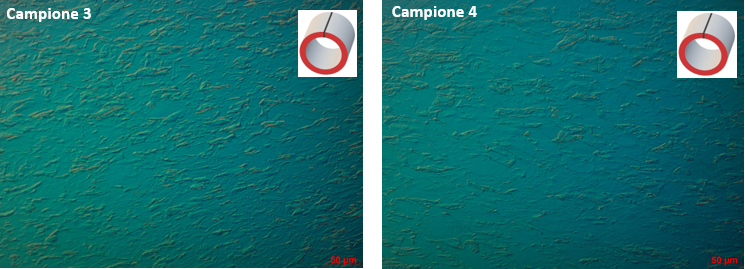
Critical element: alloy formulation
Regarding the aspect of the formulation of the alloy, it’s necessary a critical vision from who’s working because there are aspects that need to be taken under consideration which are not typical of the formulation of the alloy itself. For example, the reuse of the material, the introduction in the formulation of oxides or other elements which influence the alloy performance. It’s useful to know what is introduced and how much to what extent can the alloy be reused.
This is a case of operativeness on CNC (di operatività su CNC (numerical control machine).
It’s a750‰ red gold semifinished (tube). The alloy works correctly when the material is 100% fresh.
The problem arises when 100% scrap material is used and the burs present an unusual consumption. The material is more rigid and the CNC burs have lower tool life.
This happens because a red gold alloy, in order to achieve that color, needs a high percentage of copper inside which has the tendency to oxidize and crystallize the microstructure.
Advice: use a less percentage of scrap material to lower the crystallization effect or use an alloy with a higher silver content to lower the copper part and soften the alloy.
Critical element: alloy formulation
Formulation: critical points
These are two examples of a fine gold sheet coming from a client who didn’t know that about 300 ppm of iron and other undesired residues were present inside the two samples coming from two different production batches.
Once the presence of these residues is known, they can be accepted or not inside the formulation.
So in the «formulation» need to be considered:
- Impurities coming from the fine metal or the process
- Reused material
- Grain refiners or other additives
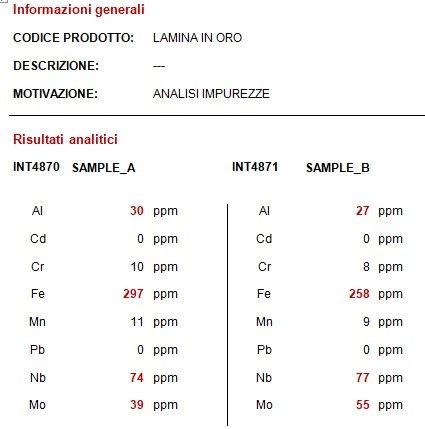
In the case 6 we have a 925‰ silver tube welded by TIG welding which, after the first two plastic deformation passages, it presented cracks along the welding line with crack openings.
We know that TIG tube performs a localized casting of the two limbs of the sheet whcih are folded and the structure is called “dendritic”.
Next we can see a phase of a thermically influenced area.
Under we see the structure, possibly equi-axial and annealed, of the initial sheet which has then undergone TIG.
The dendritic area is an area with less mechanical resistance and this, in case of an alloy with problems of impurities, can create cracks.
What can be done is to operate with a grain refiner or use an alloy with less impuritie.
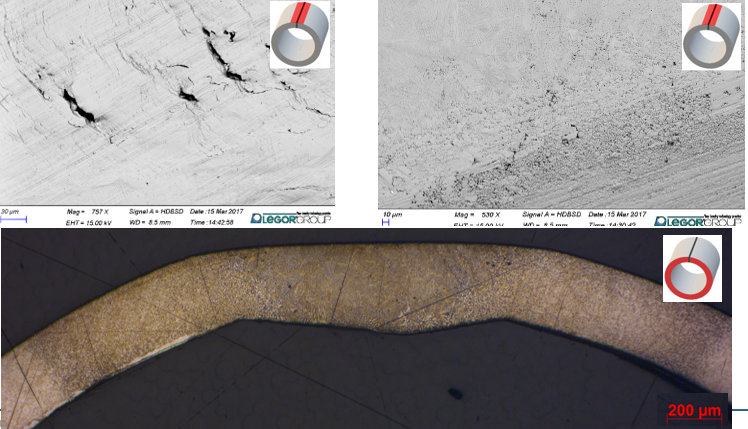
Critical element: welding process
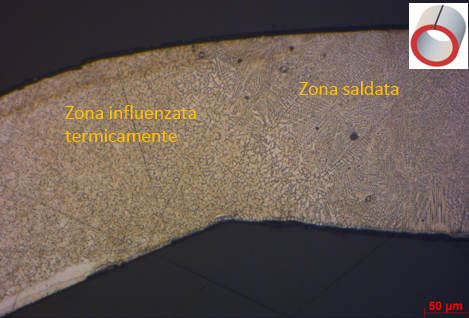
Welding: critical points
During the solidification phase, the metal undergoes a volume reduction. This generates a stress along the welding line (peak of the graphic) which generated the cracks we talked about when I further stress the tube during the drawing phase.
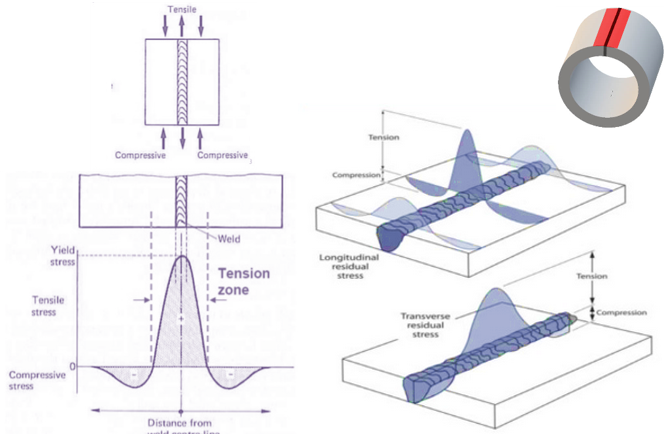
This chain, after forming and welding, (executed at liquid, without input of material) presented brittleness issues. mainly in the welding area.
The SEM analysis shows that next to the the areas where cracks are present, there are also areas that show “blowholes” due to a lack of adhesion of the two limbs of the welding.
This defect has been associated to this lack of adhesion, which could be caused by residues of welding liquid which affect the mechanical resistance of the item.
In some areas the joint wasn’t long enough to ensure mechanical resistance and this is probably due to the treatment time in the belt furnace.
The corrective action in this case is a longer time in the belt furnace.
The brittleness is visible after plating also. In case acid or other plating substances infiltrated among these cracks, there can be localized corrosions.
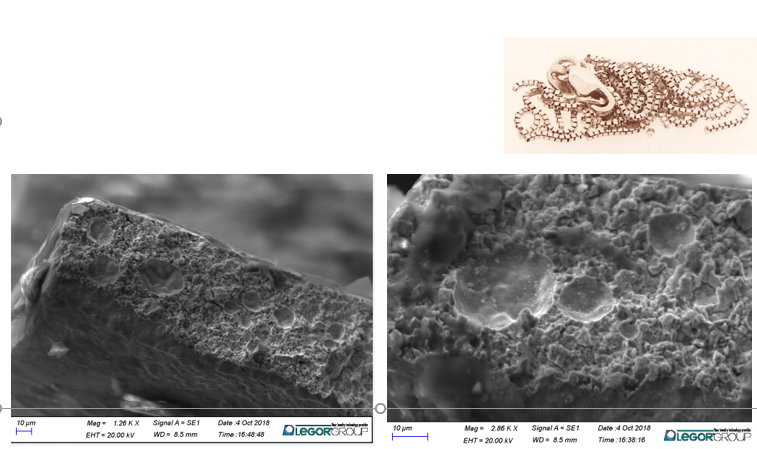
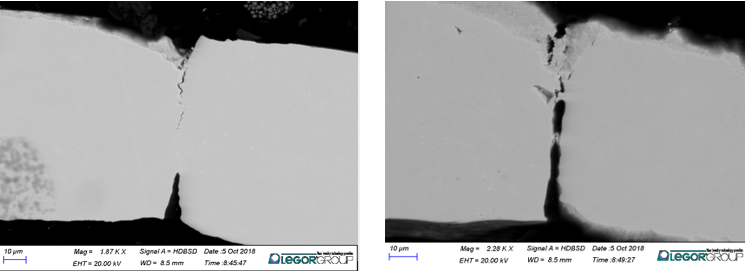
Critical element: soldering process
These three items are treated differently. Sample 1 represents the case we were presented with. After hollowing the alloy presented roughness, but it was pretty homogeneous.
After polishing through tumbling (sample 2) the SEM analysis showed areas rich in gold, but poor in silver (so a gold-copper compound) and others richer in silver. In the areas without silver, the hollowing had worked chemically causing small localized corrosions. This was probably the cause of low brightness of the item.
The corrective action has been a homogenization at 730°C for 40 minutes of the semifinished before hollowing.
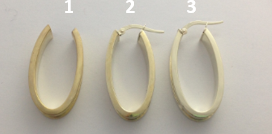
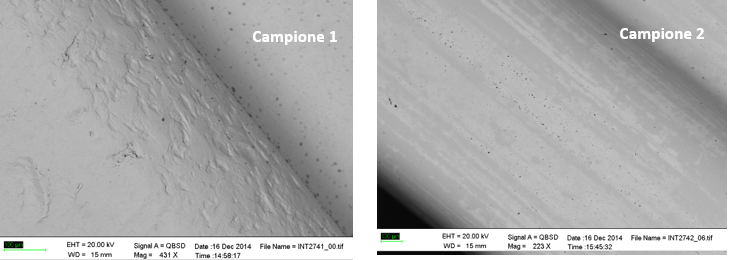
Sample 2:
Area enriched in gold and poor in silver (zone 1a, 2a): etched
Area poor in silver and correct gold title (zone 4a, 5a): unetched
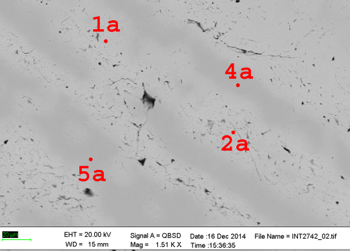
Sample 3:
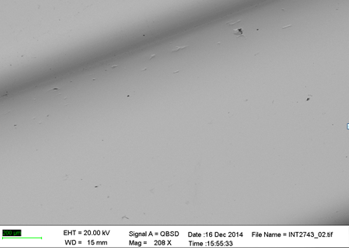
Critical Element: annealing
Annealing: what is their use?
- Residual stress elimination
- Reduction of dislocations (the linear defects which allow plastic deformation which concentrate on the grain edges and prevent further plastic deformations) inside the microstructure
- The thermal treatment is needed in order to distend these defects and start with a new, equiaxic microstructure
- If time and temperature for the transformation are excessives, there’s the risk of grain growth (it becomes less mechanically resistant)
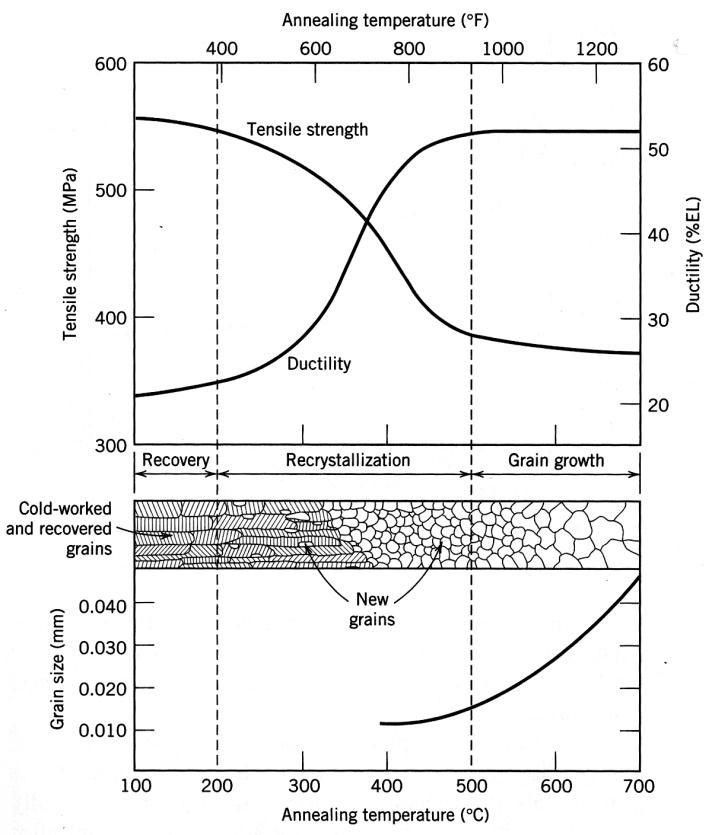
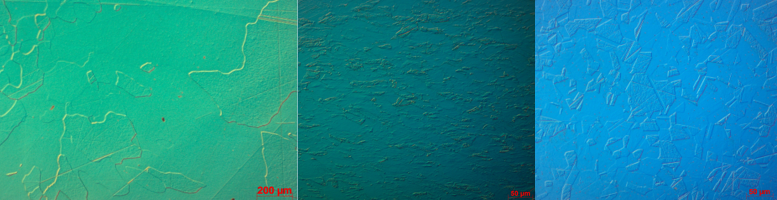
Annealing: what are the parameters to control?
The idea is to start from an initial microstructure (the semifinished from continuous casting), transforming it through plastic deformation homogeneously from the surface to the core of the metal, proceed with annealing, and then a reconstruction of the grain, generally finer, more homogeneous and with better mechanical features compared to the previous.
Two cases of 14 and 18 kt yellow gold chain with iron.
The crystalline structure is under stress before hollowing and it’s even more so in the following phases of chemical hollowing.
The rim grain is the chemically weaker part of the microstructure, the acid chemically attacked the rims, giving way to intergranular fractures.
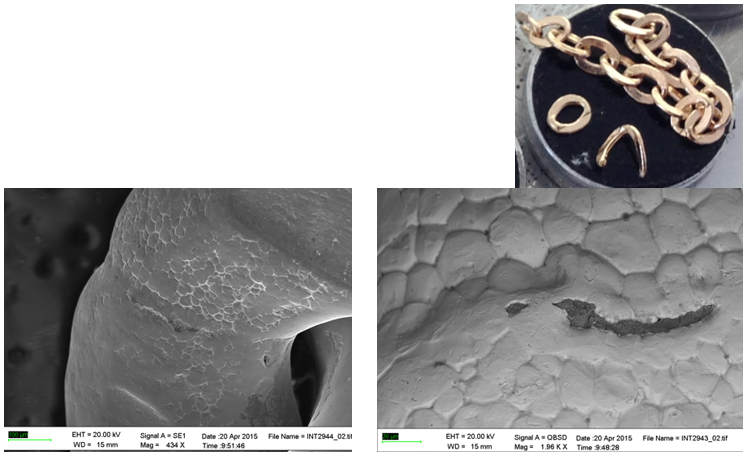
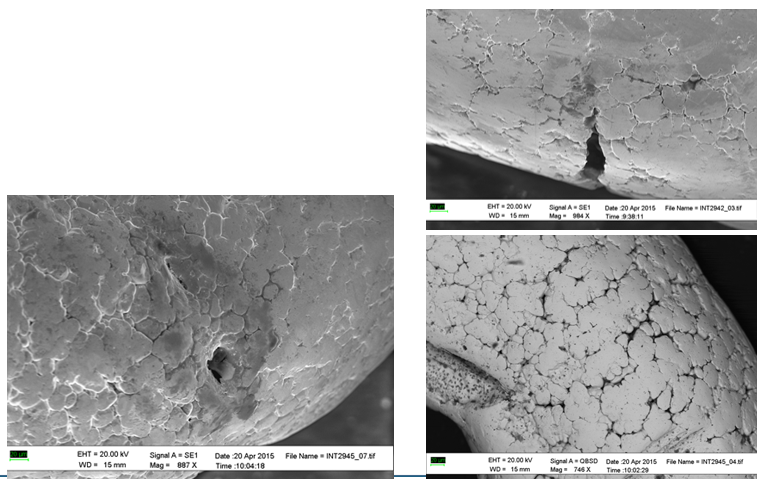
Critical points: residual stresses
Residual stresses induced by plastic deformation.
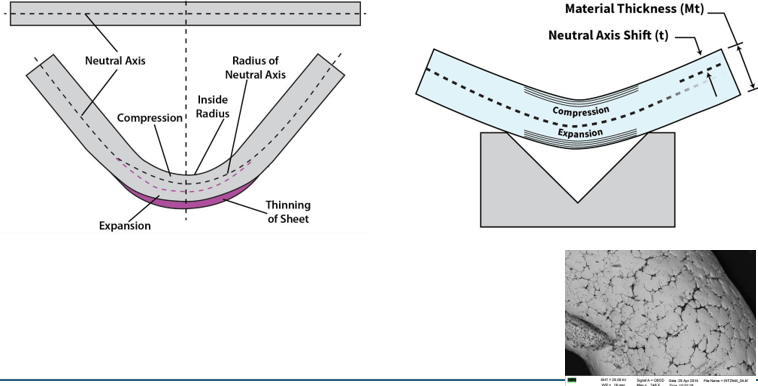
In this case the items came back from the market with cracks on some joints.
We operated some analysis in house, in particular accelerated corrosion test (artificial sweat) to highlight brittleness on the items.
Both the semifinished from which the item had been produced both the final product had undergone cracks due to coarse crystalline grains and residual stresses due to bending.
The corrective action in this case can be an easing of the item before working and a review of wire production process parameters.
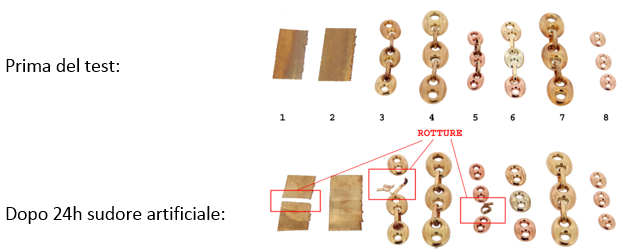
Critical element: residual stresses
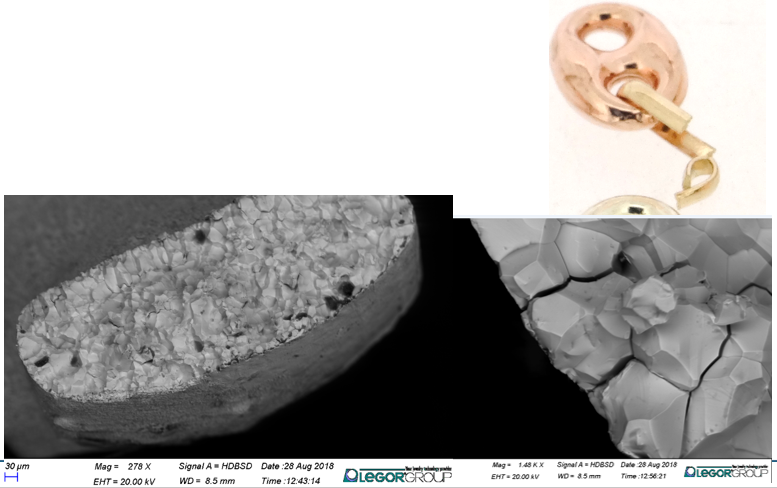
Residual stresses: what are the effects?
- They increase the risk of stress corrosion cracks (grain boundary is a weak point, stresses increase the risk)
- May modify size tolerances in items like chain links after forming, making soldering more difficult
Conclusions
It’s fundamental to have clear in mind what is the process in hand, understand what is unsatisfactory or the points which are not clear, think in terms of “respect” of alloy microstructure, rather than having quick production, evaluate starting from “standard” production steps if there are improvement possibilities.
Author

Andrea Friso
Legor Group s.p.a. – Bressanvido (VI) – Italy
Andrea Friso performs at Legor Group S.p.A. as Sales Division Manager of Master Alloys. Materials engineering graduated in 2003, he starts his cooperation with Legor Group in 2004 by writing his graduation thesis about ‘innovatively colored gold alloys’. He is the company business role operating between sales force, production and R&D, relying upon matured professional experience on the different product types and their positioning on different markets. He supports sales forces on commercial planning and the achievement of objectives together with their periodic control. He cooperates with the technical and R&D dept. as for development, enhancement and promotion of products.